Conveyor Issues – Is your belt drifting? sustaining belt damage and spilling product
By Andrew Mitchell
The belt keeps running off to one side and tripping on Belt Drift? Does this sound familiar, we look at a case study here:
- Why do we monitor belt drift
- What causes belt drift
- How do we fix it
Why do we monitor belt drift?
To protect the belt from damage, left unchecked it will drift and damage the edges and allow ingress water breaking down belt strength, and you will simply lose product off the belt, creating a mess that requires manual labour to clean up.
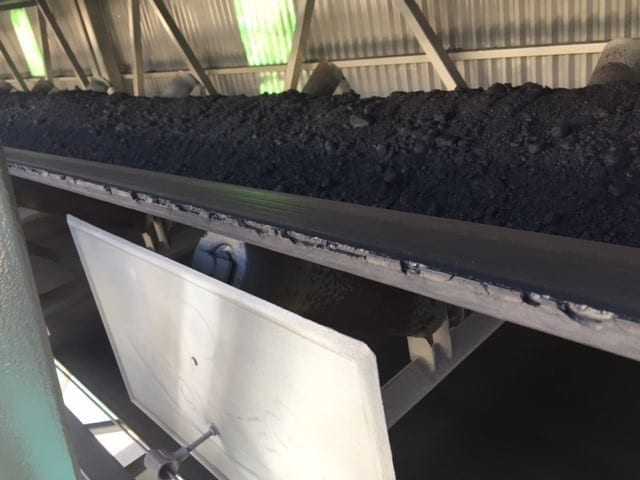
What causes belt drift?
The key reasons are as follows in order of likelihood
- The product is not loading centre of the belt
- Idlers are misaligned
- Pulleys are misaligned
- Skewed belt splice
- Insufficient belt tension, or combination of above.
How do we fix it?
Check if the belt tracks while unloaded, if it drifts only when loaded then it is likely a feed issue. Check if the belt is centre to the tail pulley as it returns, the best area to train the belt is on the return side prior to the tail pulley, if the belt centres prior to the feed chute and the product feeds centre to the belt, it will track straight.
Case study
I was asked to look at a belt drift issue on a 3 kilometre long outloading conveyor belt at a coal loading facility. The repeated trips on the belt was reducing the rate of shiploading. A plant upgrade had nameplated the system at 6000 tonnes per hour (TPH), this rate was not sustainable, at the time it was capped at 5000 TPH due to the belt drift issues
We conducted an audit on the belt and found a mismatch of steel idlers, aluminium idlers, flat return idlers, vee return idlers, tracking sets that were seized and some tied back to stear the belt. The site standard aluminium idlers were installed, the vee returns were removed to a full series of flat return and the tracking sets were serviced or replaced to ensure they functioned as per design.
We then conducted a full survey of the belt do verify if alignment was an issue, a number of areas were rectified during the survey however the pulleys were in acceptable alignment based on the theoretical centreline.
It became apparent the main contributor was the transfer point onto the belt; the product stream started at a surge bin through a set of vibrating feeders via a deflector plate at right angles to an intermediate feed belt. By design this is not an ideal method of product transfer, refer below third party review of feeder transfer.
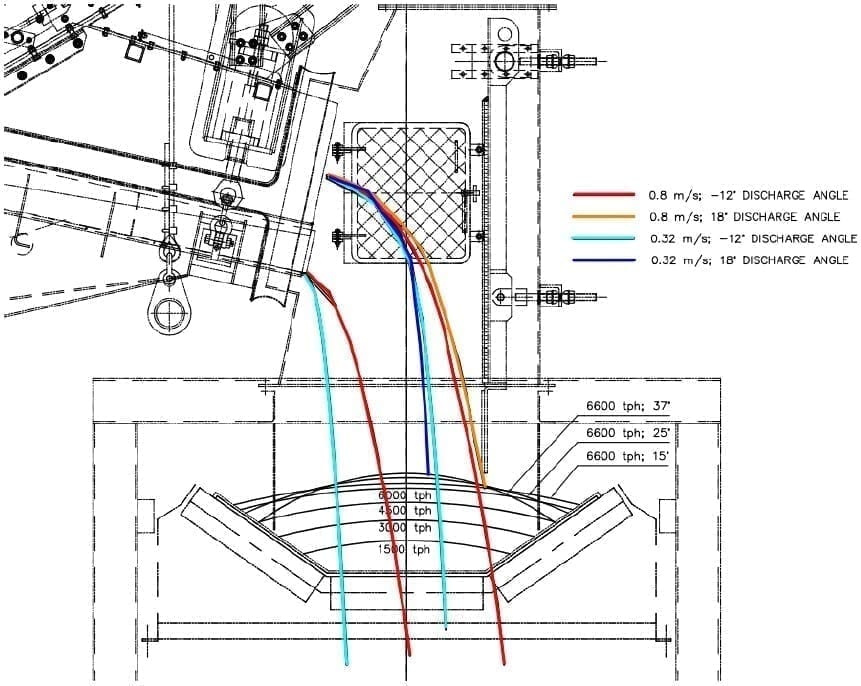
Feeder Chute
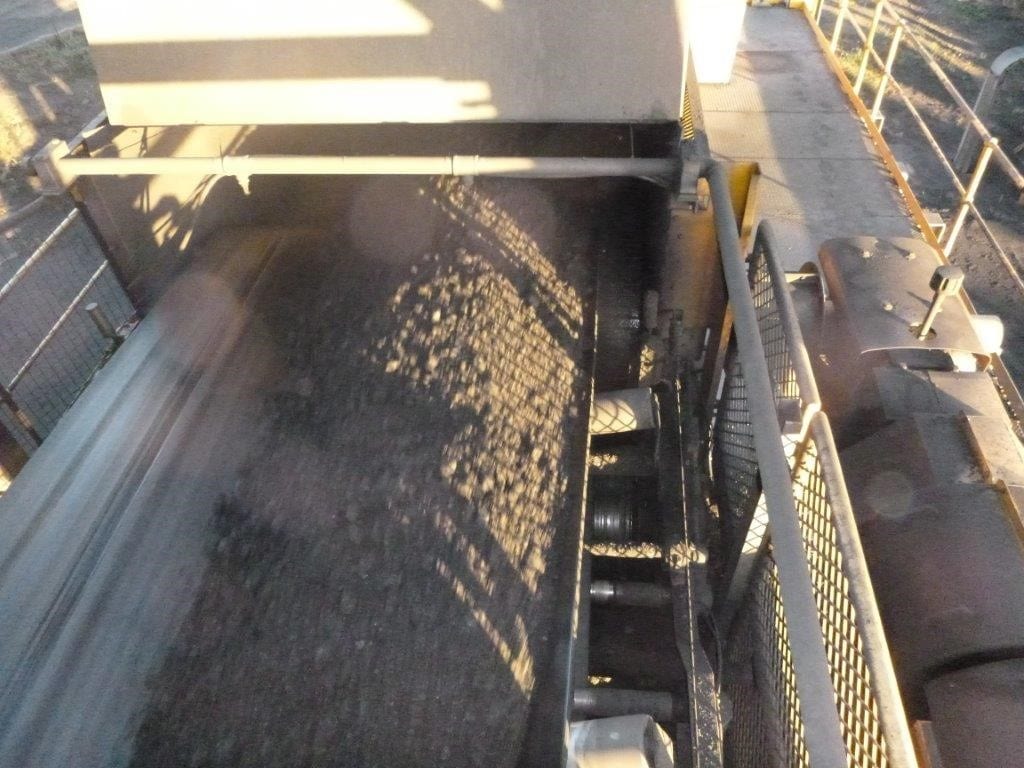
The belt pictured above then transferred through a sample plant tower at right angles onto the outloading belt. A third party review of the transfer point using Discrete Element Modelling (DEM) was conducting to simulate the start-up of the product stream
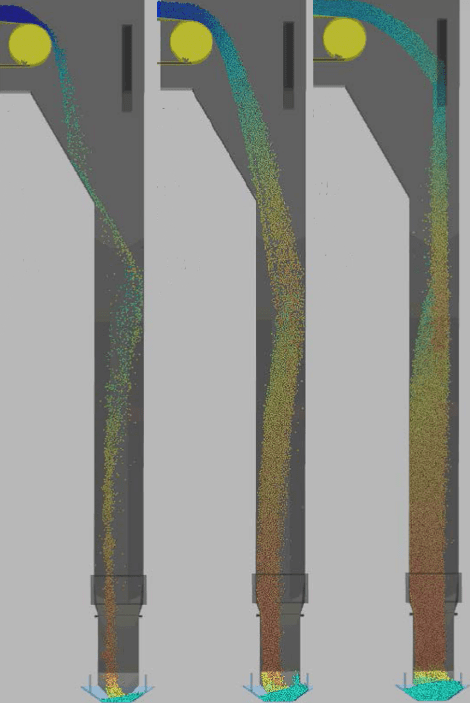
The model was then compared to actual video footage to verify results.
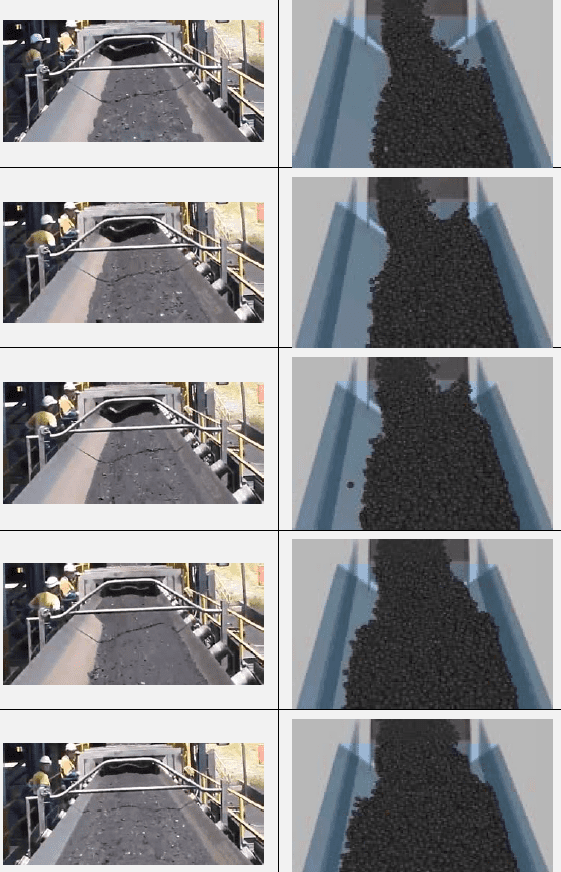
Again changes in this area required major upgrades, smaller incremental changes were investigated and implemented.
Rubber coated impact idlers were installed directly under the transfer point, this increased friction between idlers and belt, holding centre for a longer duration, this decreased the belt drift but did not eliminate it.
It was suggested a number of times to increase counterweight mass, a third party consultant was engaged to review the design. Theoretically, the calculations indicated there would be no performance benefit in increasing the counterweight from 14.3 tonne (T) however the infrastructure could safely accept an increase.
The existing mass weighed in at 11.9 T (under design) an additional 4.6 T was added to bring it up to 16.5T.
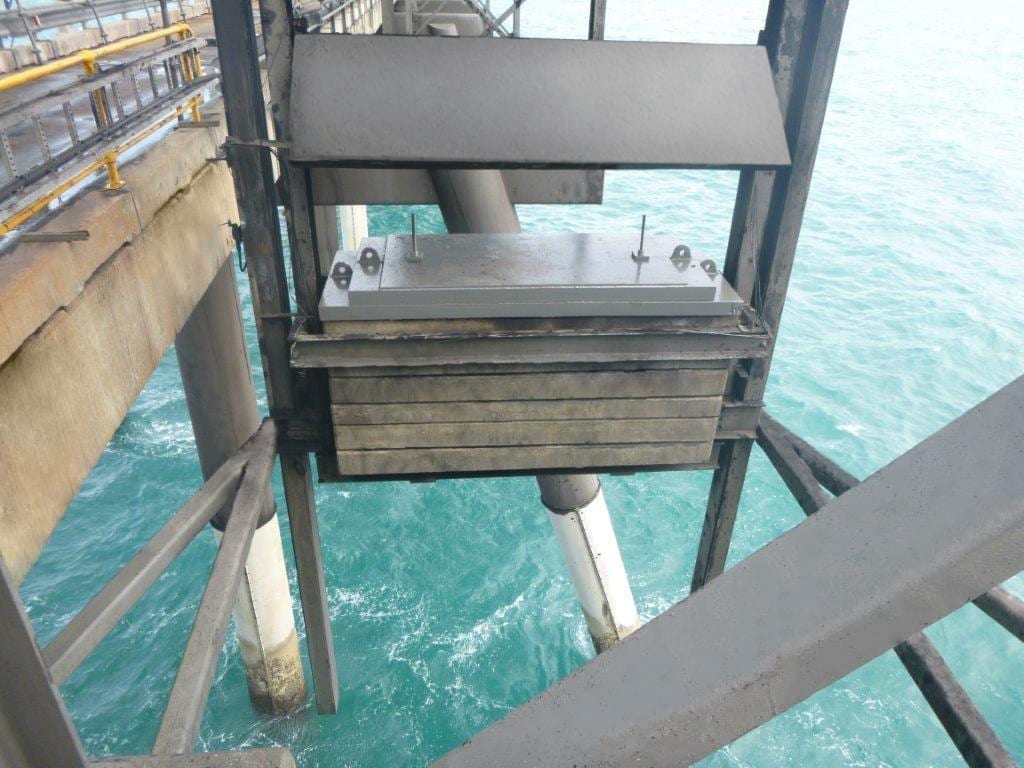
It turned out that the increased belt tension along with the other works was enough to overcome the belt drift and allow the stream to consistently run at 6000 TPH with minimal capital expenditure.
Feel free to contact me if you would like any further information on how we can help maximise your plant throughput, I hope you enjoyed this share.
Please read our previous article Conveyor Issues- Is your belt slipping and plant rate suffering?
Please feel free to request more information below.
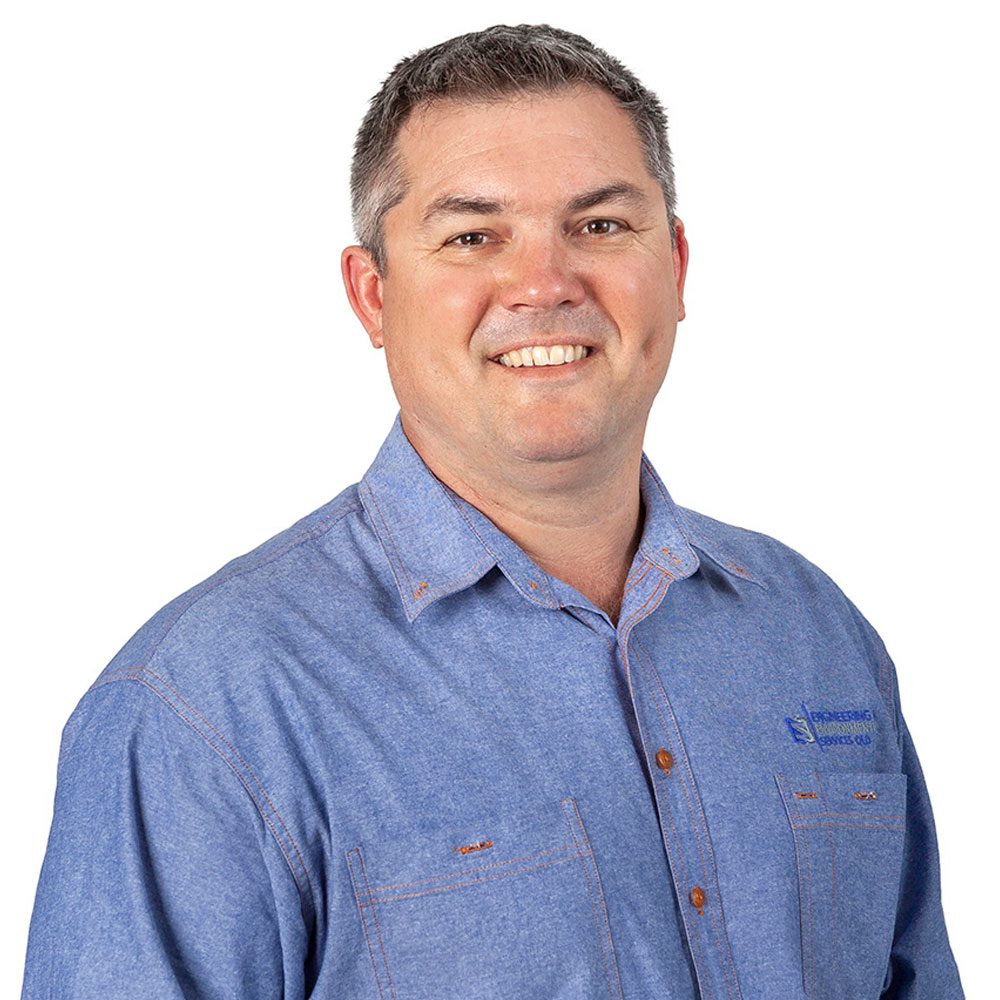
Andrew Mitchell is Principal Engineer at Engineering & Environmental Services. He designs, engineers, and delivers projects in the resource industry aimed at maximising your business benefits.