Conveyor Issues- Are you getting excessive top cover wear?
By Andrew Mitchell
The tail end skirts are failing prematurely and we’re getting excessive top cover wear on the belt? Does this sound familiar; we look at a case study here:
- Why do we need transfer chutes
- What causes skirt failure and high wear rates at the transfer point
- How do we fix it
Why do we need transfer points?
A transfer chute generally directs the product from the head of one conveyor to tail end of another conveyor in most cases to change the direction of product flow through a processing plant. Without considerable design intent there is potential risk for the chute to become a bottleneck and not efficiently move material from one conveyor to the next.
What causes skirt failure and high wear at the transfer point?
Wear is associated with the deceleration of material as it passes through the transfer point and the contact made with a surface (conveyor) travelling at a faster rate.
Traditionally chutes have been characterised by only having flat surfaces and minimal steel work using simple shapes to direct material from one conveyor to the next.
Transferring coal from a vertical drop to horizontal speed of around 5m/s creates considerable drag, material build up and pressure on the skirts.
How do we fix it?
I was asked to look at a Stacker Reclaimer at coal loading facility where the elevating conveyor transferred 6000 TPH of coal onto the slewing boom belt travelling at approximately 5.2 m/s. Unwanted coal spillage was coming from the tail end skirted region of the boom belt, contributing to coal build up on machine and bund.
A “soft boot” solution was determined; however, the original concept overlooked the requirement for a modified head chute deflector to compliment the coal flow. Soft flow chutes are characterised by curved surfaces that catch and redirect the flow of material. A soft flow chute will typically consist of two curved sections called a hood and a spoon, refer https://www.bulkhandlingreview.com.au/problems-with-short-drop-height-soft-flow-chutes.
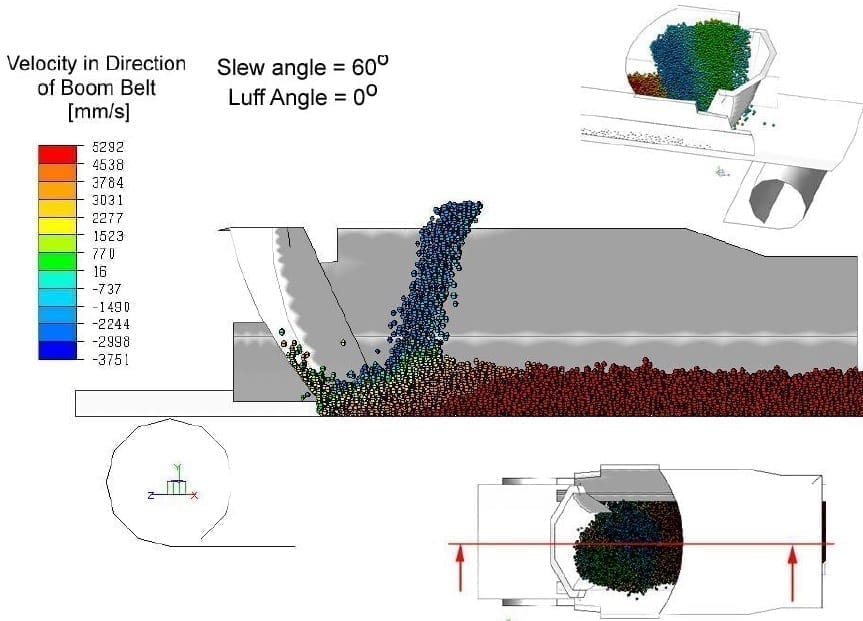
A third party design consultant conducted a Discrete Element Modelling (DEM) analysis on the concept and found that the “soft boot” (spoon) position was incorrect and the deflector plate was not directing the coal on to the spoon. Further analysis determined that modifying the geometry of the spoon and incorporating a new deflector plate would improve the speed of the coal through the transfer chute.
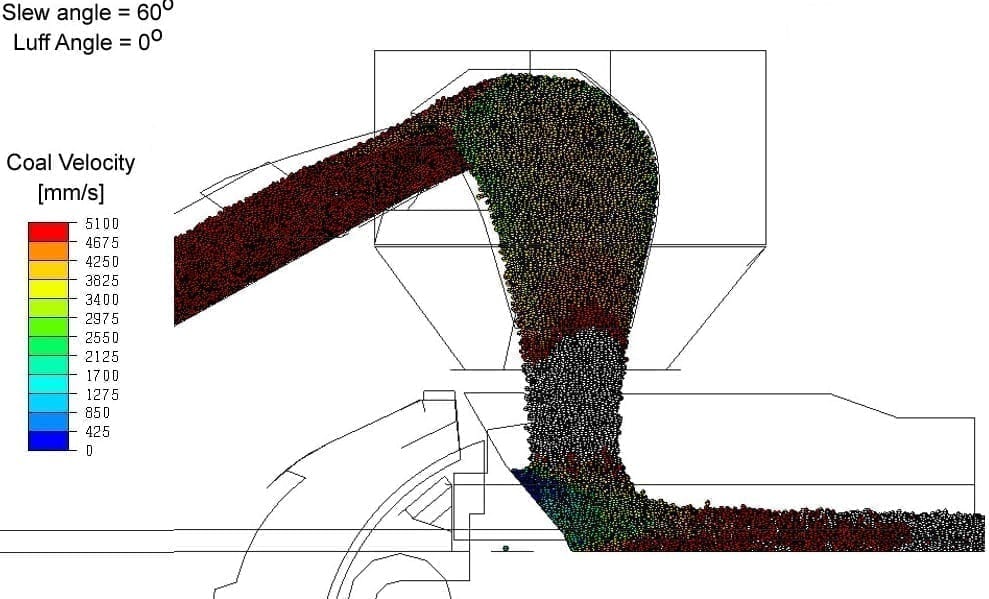
Based on the findings a complete set of fabrication drawings were created and components fabricated in the workshop.

The new deflector plate and spoon were installed during the annual Stacker Reclaimer shutdown.

The chutes performance was then monitored and improvements recognised in the following areas:
- Reduced skirt wear;
- Reduced belt wear;
- Reduced spillage and build up on the machine; and
- Reduced spillage and build up on the bund.
Feel free to contact me if you would like any further information on how we can help reduce your maintenance costs, I hope you enjoyed this share
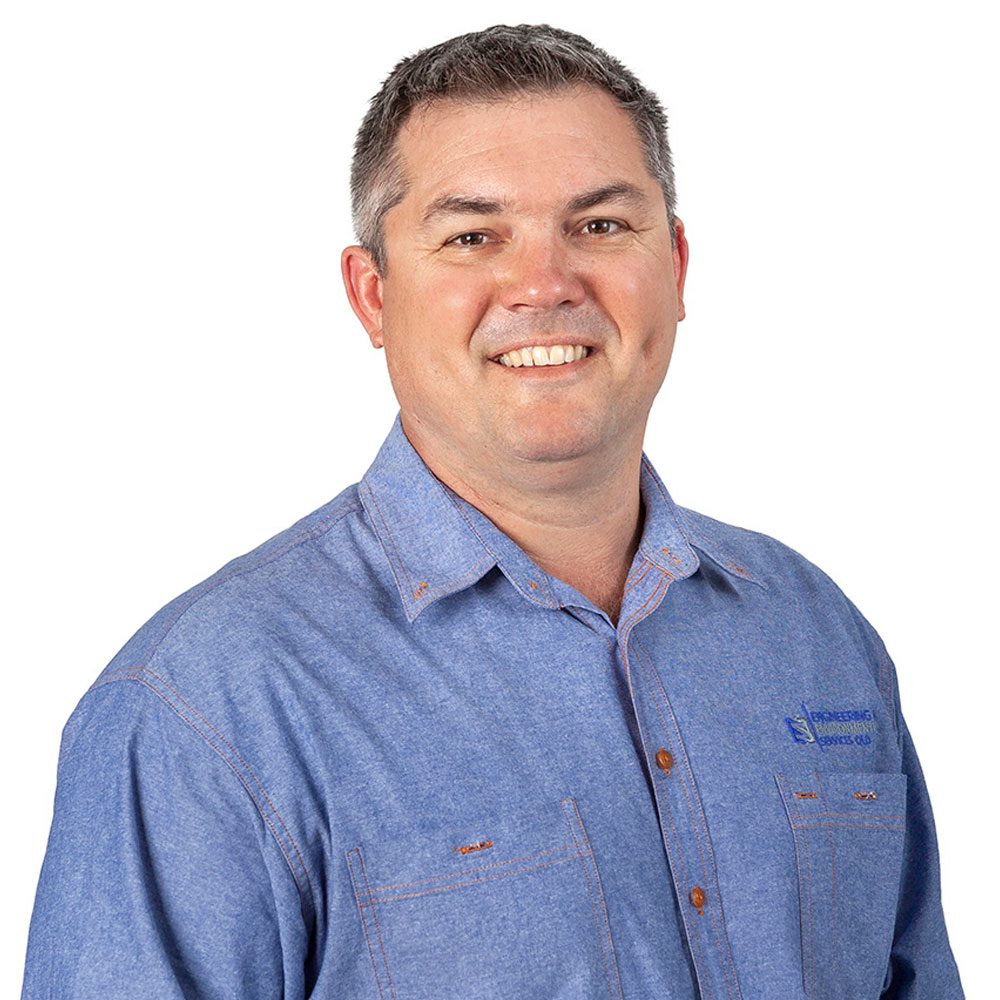
Andrew Mitchell is Principal Engineer at Engineering & Environmental Services. He designs, engineers, and delivers projects in the resource industry aimed at maximising your business benefits.